-
Services
We manufacture metal and plastic components with complex geometries and high precision requirements. Our automated processes enable efficient deliveries even for large volumes.
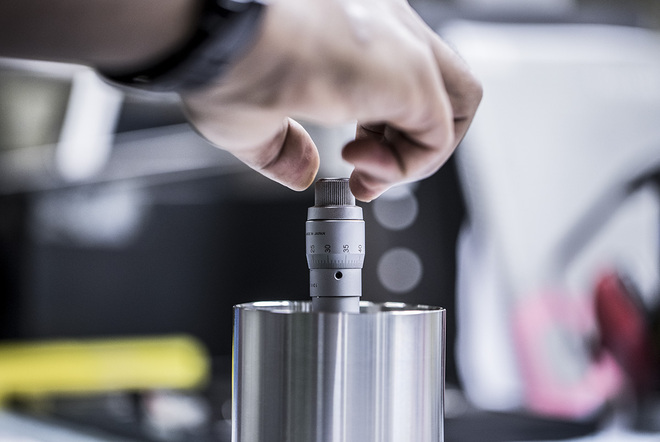
Industries with high demands
The parts we manufacture are often used in the medical technology industry and other industries where people’s lives and health could be jeopardized if the products do not work optimally.
Therefore, extreme accuracy and precision are alfa and omega in our production processes. Our customers can always trust that they will get exactly what is promised. We take our work very seriously.
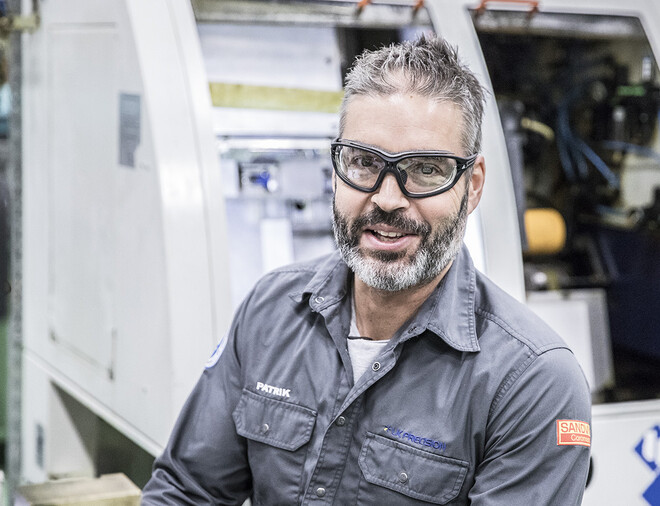
Prototype or full-scale production?
We have the capacity for high-volume production while meeting the highest performance standards. We always focus on our customer’s needs and wishes, and we can be your partner from product development via prototype production to full-scale production. Examples of our services include:
- Project management
- Product development (DFM/DFA)
- Knowledge of materials
- Tool making
- Preparation
- Production
- Measurement room services
- Assembly
- Manual processing
- Warehousing
- Labeling, cleaning and packaging
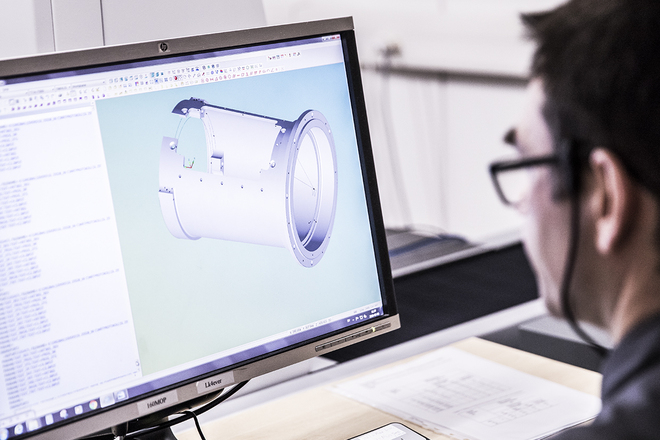
From idea to finished product
We follow the product from the idea stage and all the way to the finished product. By being involved in the process right from the drawing board, we ensure that the product is producible and that all our customer’s requirements and expectations are met. With our internally developed process control, we can ensure that the products go from the prototype stage to series production in a smooth and cost-effective way.
PLUPP – the path from prototype to series production
#1 |
#2 |
#3 |
#4 |
#5 |
#6
|